Selection of Cold Work Tool Steels
Cold work tool steels are designed for tooling applications where the service temperature is under about 600°F (316°C). In selecting cold work tool steels, the metallurgical factors that ultimately affect tool performance and longevity must be considered. These include hardness and strength, toughness, and wear resistance. Hardness and strength are in a commensurate relationship; the higher the hardness, the higher the strength. Higher hardness also generally corresponds with higher wear resistance. However, high hardness and strength typically also correspond with lower toughness, or in other words, less resistance to cracking from impact or sudden shock loading. The specific hardness, wear, and toughness requirements of the application determine which tool steel should be used. For new tooling applications, the selection normally involves some degree of trial and error to determine which tool steel provides the best combination of properties for the most cost effective tooling performance.
The nominal chemical compositions of the common cold work tool steels are presented in weight percent below. Relative comparisons of the properties of the steels are presented in the chart on the reverse side. More specific information about the steels may be obtained from the individual data sheets. M2 high-speed steel and H13 hot work steel are included in the property comparisons because both are sometimes used in cold work tooling applications and to provide a common reference for comparisons with the properties of the high-speed and hot work tool steels.
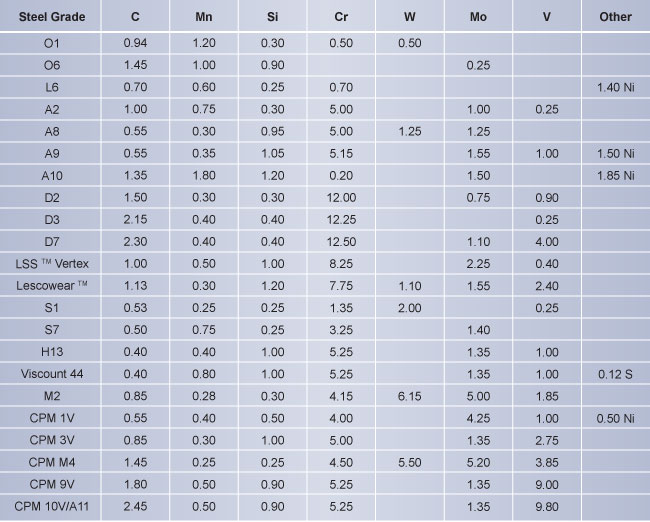
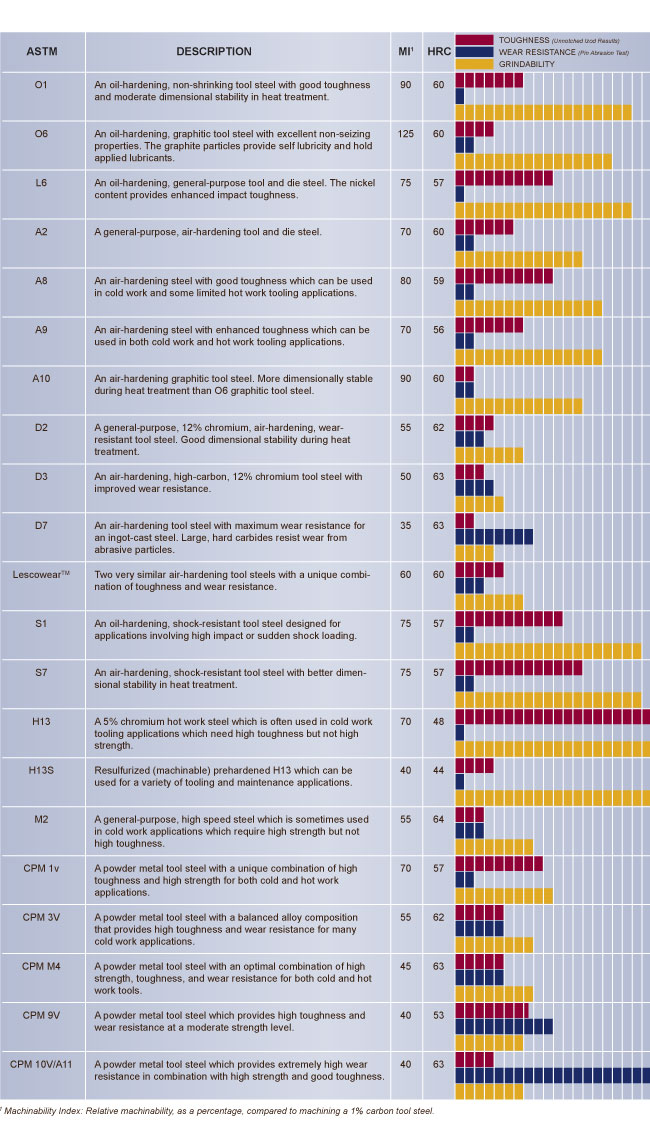