CPM 1V Powder Metal Tool Steel
CPM 1V tool steel is a medium-carbon, powder metallurgy tool steel that exhibits very high impact toughness. The unique chemical composition results in tooling which has an outstanding combination of properties including very high impact toughness, very good hot hardness, and good wear resistance. The impact toughness is enhanced by the fine grain size, small carbides, and superior cleanliness of the pwder metallurgy (PM) microstructure.
Typically, when selecting a tool steel, one must choose between high strength or high toughness, with a compromise in the other of these two properties. However, with an attainable hardness in the low 60's Rockwell C, the unique properties of CPM 1V make it an excellent choice for tooling applications that require both high strength and high impact toughness, heat resistance, or all of the above.
APPLICATIONS: CMP 1V should be considered for service in blanking dies, sizing dies, shear blades, cold and hot forging punches, forging dies, gear rolling dies, and many other applications where a combination of strength and toughness is required. CPM 1V should also be considered for severe applications where only steels such as S7, A9, and the high-alloy hot work steels have been suitable.
Composition
C | Mn | Si | Cr | W | Mo | V |
0.55 | 0.40 | 0.50 | 4.50 | 2.15 | 2.75 | 1.00 |
Relative Properties
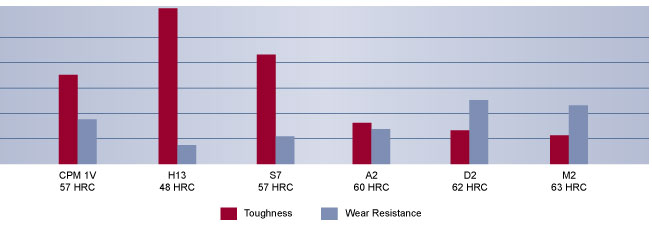
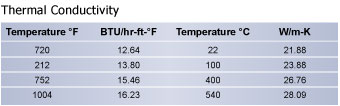
Physical Properties
- Density: 0.284 lb/in3 (7850 kg/m3)
- Specific Gravity: 7.80
- Modulus of Elasticity: 30 x 106 psi (207GPa)
- Machinability: 65-70% of a 1% carbon steel
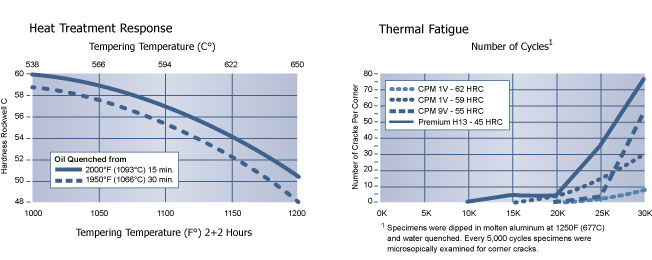
Heat Treating Instructions
Hardening
Preheating: 1500-1550°F (816-845°C), equalize.
Austenitizing (High Heat): Heat rapidly from the preheat.
Furnace: 1950-2025°F (1066-1107°C)
Salt Bath: 1925-2000°F (1052-1093°C)
Quenching: Pressurized gas, warm oil, or air.
For pressurized gas, a quench rate of approximately 400°F (222°C) per minute to below 1000°F (538°C) is critical to obtain the desired properties.
For oil, quench until black, about 900°F (482°C), then cool in still air to 150-125°F (66-51°C).
Tempering: Temper immediately after quenching. Typical temperature range is 950-1100°F (510-593°C). Do not temper below 950°F (510°C). Hold at temperature for 2 hours then air cool to ambient temperature. Double tempering is required. Triple tempering is recommended if tools will be wire EDM'd from asolid block after heat treatment.
Annealing
Annealing must be performed after hot working and before rehardening.
Heat at a rate not exceeding 400°F per hour (222°C per hour) to 1575-1600°F (854-871°C), and hold at temperature for 1 hour per inch of maximum thickness; 2 hours minimum. Then cool slowly with the furnace at a rate not exceeding 50°F per hour (28°C per hour) to 1000°F (538°C). Continue cooling to ambient temperature in the furnace or in air. The resultant hardness should be a maximum of 255 HRW.
*CPM, 1V, 3V, 9V, 10V, 15V, S30V, S90V, Rex M4, Rex T15, and Rex 76 are trademarks of Crucible Industries LLC