CPM 9V Powder Metal Tool Steel
CPM 9V is a powder metal tool steel that provides very high wear resistance in combination with high impact toughness. A large volume of hard vanadium carbides provides the high wear resistance. CPM 9V contains less carbon and vanadium than CPM 10V, which results in a lower attainable hardness, slightly lower wear resistance, but a significant increase in toughness. The lower carbon content also enables CPM 9V to be used in warm and hot work applications where resistance to thermal fatigue cracking is important. CPM 9V may be used in unique tooling applications for improved toughness compared to CPM 10V and high-speed steels, and improved wear resistance compared to D2 and other tool steels.
APPLICATIONS: CPM 9V is widely used for plastic injection feed screws, non-return valves, shear blades, and forging dies.
Composition
C | Mn | Si | Cr | Mo | V |
1.90 | 0.50 | 0.90 | 5.25 | 1.30 | 9.10 |
Relative Properties

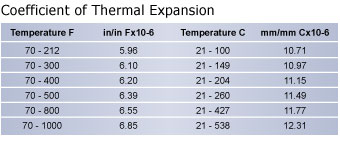
Physical Properties
- Density: 0.267 lb/in3 (7418 kg/m3)
- Specific Gravity: 7.41
- Modulus of Elasticity: 32 x 106 psi (221GPa)
- Machinability: 35-40% of a 1% carbon steel
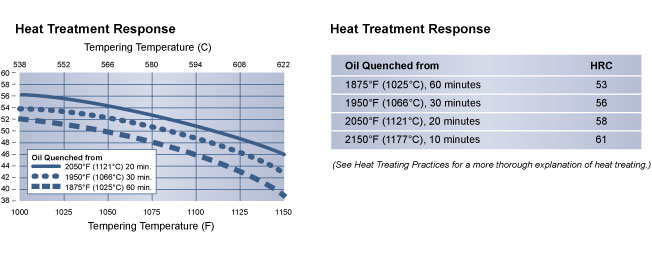
Heat Treating Instructions
Critical Temperature: Ac1: 1590°F (866°C)
Hardening
Preheating: 1500-1550°F (816-845°C), equalize.
Austenitizing (High Heat): Heat rapidly from the preheat, typically by transferring to a second furnace.
For Higher Wear Resistance:
Furnace or Salt Bath: 2050°F (1121°C)
Soak for 25 minutes minimum at temperature
For Balance of Wear Resistance and Toughness:
Furnace or Salt Bath: 1950-2000°F (1066-1093°C)
Soak for 25 minutes minimum at temperature
For Maximum Toughness and minimum distortion in cooling:
Furnace: 1900°F (1038°C)
Salt Bath: 1875°F (1025°C)
Soak for 45 minutes minimum at temperature
Quenching: Air, pressurized gas, warm oil, or salt. Warm oil or salt bath quenching will give maximum hardening response. For pressurized gas, the furnace should have a minimum quench pressure of 4 bars. The quench rate to below 1000°F (538°C) is critical to obtain the desired properties.
For oil, quench until black, about 900°F (482°C), then cool in still air to 150-125°F (66-51°C). For salt maintained at 1000-1100°F (538-593°C), equalize in the salt, then cool in still air to 150-125°F (66-51°C).
Tempering: Temper immediately after quenching. Typical temperature range is 1000-1100°F (538-593°C). Do not temper below 1000°F (538°C). Hold at temperature for 2 hours then air cool to ambient temperature. Double tempering is required. Triple tempering is required when austenitzed above 2050°F (1121°C).
Annealing
Annealing must be performed after hot working and before rehardening.
Heat at a rate not exceeding 400°F per hour (222°C per hour) to 1600-1650°F (871-899°C), and hold at temperature for 1 hour per inch of maximum thickness; 2 hours minimum. Then cool slowly with the furnace at a rate not exceeding 30°F per hour (17°C per hour) to 1000°F (538°C). Continue cooling to ambient temperature in the furnace or in air. The resultant hardness should e a maximum of 277 HBW.
*CPM, 1V, 3V, 9V, 10V, 15V, S30V, S90V, Rex M4, Rex T15, and Rex 76 are trademarks of Crucible Industries LLC