Data Sheet - A2
Typical Composition | ||||
C | Mn | Cr | Mo | V |
1.00 | 0.85 | 5.25 | 1.10 | 0.25 |
A2 is an air-hardening medium alloy tool steel which is heat treatable to HRC 60-62. It has wear resistance intermediate between the oil hardening tool steels (O1) and the high carbon chromium tool steels (D2). Because it offers a combination of good toughness along with moderate wear resistance, it has been widely used for many years in variety of cold work applications which require fairly high abrasion resistance but where the higher carbon/ high chromium steels are prone to chipping and cracking. A2 is quite easily machined in the annealed condition and, like other air-hardening tool steels, exhibits minimal distortion on hardening, making it an excellent choice for dies of complicated design.
The typical applications include punches and dies, wear parts, blanking dies, shear blades, coining dies, industrial knives/slitters, forming dies, scrap choppers, fine blanking dies, gauges, lamination dies, tablet compression tooling, trim dies, and mold inserts.
Mechanical Properties | |||||
---|---|---|---|---|---|
Heat Treatment Austenitizing Temp. |
HRC | Impact Toughness ft.-lb. (J) | Wear Resistance Adhensive | ||
AIRKOOL | 1750°F(955C) | 60 | 40 | (53) | 2-3 |
S7 | 1750°F(955C) | 57 | 125 | (165) | 1 |
D2 | 1850°F(1065C) | 60 | 21 | (28) | 3-4 |
Cru-Wear | 1950°F(1065C) | 62 | 30 | (40) | 5-6 |
3V | 1950°F(1065C) | 60 | 70 | (95) | 7 |
M2 | 2050°F(1120C) | 62 | 20 | (27) | 8-10 |
M4 | 2050°F(1120C) | 62 | 32 | (43) | 20-25 |
10V | 2150°F(1175C) | 63 | 14 | (19) | 90 |
Machinability
The Machinability of A2 as annealed is about 50% of W1 tool steel.
Surface Treatments
A2 can be given standard surface treatments such as nitriding TiN (titanium nitride) coating or hard chrome plating if desired. When using surface treatments, harden from the high side of the austenitizing range and temper at or above the process temperature of the treatment.
This data sheet is for informational purposes only. Alloy characteristics are subject to change due to chemical composition and/or processing. We do not certify the material’s suitability for specific applications.
Thermal Treatments
Annealing: Heat to 1600°F (870°C), hold 2 hours, slow cool 50°F (30°C) per hour to 1200°F (650°C) then air cool. OR heat to 1600°F (870°C), hold 2 hrs, cool to 1400°F (760°C) hold 6 hrs. then air cool.
Annealed Hardness: About BHN197/241
Stress Relieving
Annealed Parts: Heat to 1200-1250°F (650-675°C), hold 2 hours, then cool in still air
Hardened Parts: Heat to 25-50°F (15-25°C) below the original tempering temperature, hold 2 hours, then cool in still air.
Hardening
Preheat: Heat to 1100-1250°F (595-675°C), equalize, then to 1350-1450°F (730-790°C), equalize.
Austenitize: 1750-1800°F (955-980°C), Hold time at temperature 30-45 minutes.
Quench: Air or positive pressure quench (2 bar minimum) to below 150°F (65°C).
Temper: 400-1000°F (205-540°C).Temper 2 hours minimum each time or at least 1 hour per inch (25mm) of thickness. Double temper. Cool to room temperature in between tempers.
Cryogenic Treating: Refrigeration after the first temper may improve long term dimensional stability by transforming retained austenite. Any refrigeration treatment must be followed by a temper.
Hardening Temperature | Tempering Temp. | HRC | Longitudinal Size Change |
1775°F(970C) | 400°F(205C) | 61 | +0.07% |
1775°F(970C) | 500°F(260C) | 59 | +0.10% |
1775°F(970C) | 600°F(315C) | 58 | +0.09% |
Heat Treat Response Hardness Impact Toughness Data |
|||
Austenitized 1775°F(970C) Air Cool | |||
Tempering | HRC | Charpy C-Notch | |
Temp. | Ft.-lb | (J) | |
As Air Quenched | 64 | ||
300°F(150C) | 62 | ||
400°F(260C) | 61 | 31 | 42 |
500°F(260C) | 60 | 41 | 56 |
600°F(315C) | 59 | 37 | 50 |
700°F(370C) | 58 | 33 | 45 |
800°F(420C) | 58 | 31 | 42 |
900°F(480C) | 58 | 29 | 39 |
1000°F(540C) | 55 | 41 | 56 |
1100°F(595C) | 51 |
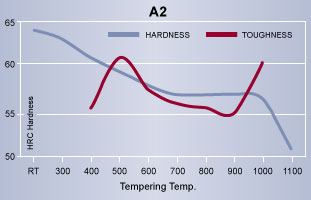
Welding
Use air hardening tool steel filler material.
Annealed Material: Preheat 700-900°F (370-480°C); maintain the temperature of the work piece above 700°F (370°C) during welding. After welding, reanneal or temper at 1400°F (760°C) for 6 hours.
Hardened Material: Preheat 25-50°F (15-30°C) below original tempering temperature or 300°F (150°C) minimum.