A6 Tool Steel
A6 Tool Steel is a medium-alloy, air-hardening tool steel that is characterized by its ability to be through hardened while using the low austenitizing temperatures which are typically associated with oil-hardening tool steels. It exhibits good toughness and excellent dimensional stability in heat treatment. A6 is intermediate in wear resistance between O1 oil-hardening tool steel and D2 high-carbon, high-chromium tool steel.
APPLICATIONS: Blanking and forming dies, trim dies, bending and forming tools, mandrels, chuck jaws, tooling for plastic injection molding, dowel pins, shear knives, and gauges.
Composition
C | Mn | Si | Cr | Mo |
0.70 | 2.00 | 0.30 | 1.00 | 1.25 |
Relative Properties
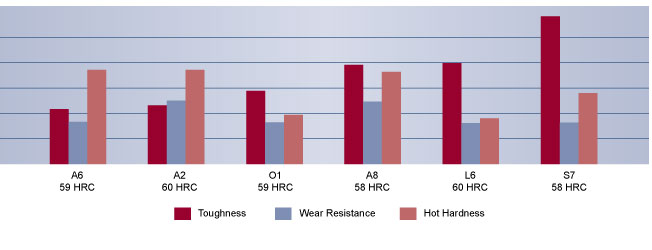
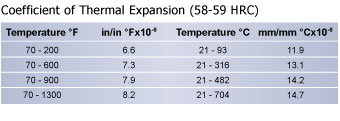
Physical Properties
- Density: 0.283 lb/in3 (7833 kg/m3)
- Specific Gravity: 7.83
- Modulus of Elasticity: 30 x 106 psi (207GPa)
- Machinability: 80% of a 1% carbon steel
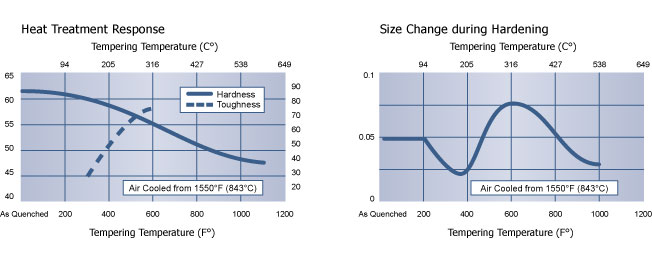
Heat Treating Instructions
Hardening
Critical Temperature: Ac1: 1340ºF (727ºC)
Preheating: Heat at a rate not exceeding 400ºF per hour (222ºC per hour) to 1200-1300ºF (649-704ºC) and equalize.
Austenitizing (High Heat): Heat slowly from the preheat. Furnace or Salt: 1525-1625ºF (829-885ºC) Soak for 30 minutes for the first inch (25.4 mm) of thickness, plus 15 minutes for each additional inch (25.4 mm).
Quenching: Air or pressurized gas to 150-125ºF (66- 51ºC). Sizes up to 4 inches (101.6 mm) in thickness will through harden when air cooled from 1575ºF (857ºC). Sizes up to 6 inches (152.4 mm) in thickness will through harden when air cooled from 1625ºF (885ºC).
Tempering: Temper immediately after quenching. Hold at temperature for 1 hour per inch (25.4 mm) of thickness, 2 hours minimum, then air cool to ambient temperature. The typical tempering range is 350 to 400ºF (177 to 204ºC).
To minimize internal stresses in cross sections greater than 6 inches (152.4 mm) and to improve stability in tools that will be EDM'd after heat treatment, a soaking time of 4 to 6 hours at the tempering temperature is strongly recommended.
Cryogenic Treatment: Some prefer to do cryogenic treatment as an extension of the quench from the austenitizing treatment. Others prefer to cryogenically treat after tempering.
Annealing
Annealing must be performed after hot working and before re-hardening.
Heat at a rate not exceeding 400ºF per hour (222ºC per hour) to 1370ºF (743ºC), and hold at temperature for 1 hour per inch (25.4 mm) of maximum thickness; 2 hours minimum. Then cool slowly with the furnace at a rate not exceeding 20ºF per hour (11ºC per hour) to 950ºF (510ºC). Continue cooling to ambient temperature in the furnace or in air. The resultant hardness should be a maximum of 248 HBW.