A7 Wear-Resistant Tool Steel
A7 Wear-Resistant Tool Steel is a chromium-modified A7 type air-hardening tool steel that exhibits exceptional wear resistance. The high carbon and vanadium contents result in numerous, hard vanadium carbide particles in the steel. These carbides exhibit a hardness that is equivalent to approximately 80 to 85 Rockwell C. Resists wear from sliding contact with other steels as well as from contact with dry and wet slurries of hard abrasive particles such as sand, shot blast media, and ceramics.
APPLICATIONS: Brick mold liners, sand slinger liners, shot blasting equipment liners, extrusion tools for ceramics, powder compaction tooling, and machine tool ways.
Composition
C | Mn | S | Si | Cr | Mo | V |
2.60 | 0.60 | 0.005 max | 0.30 | 8.25 | 1.20 | 4.50 |
Relative Properties
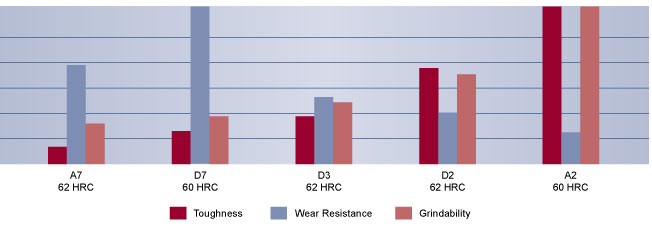
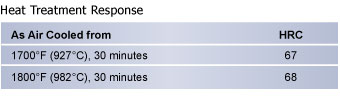
Physical Properties
- Machinability: 20-25% of a 1% carbon steel
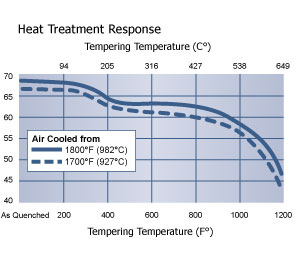
Heat Treating Instructions
Hardening
Critical Temperature: Ac1: 1340ºF (727ºC)
Preheating: Heat at a rate not exceeding 400ºF per hour (222ºC per hour) to 1200-1300ºF (649-704ºC) and equalize.
Austenitizing (High Heat): Heat rapidly from the preheat. Furnace or Salt: 1700-1800°F (927-982°C). For maximum toughness, use 1700°F (927°C). For maximum wear resistance use 1800°F (982°C).
Soak at temperature for 15 minutes per inch (25.4 mm) of thickness; 30 minutes minimum.
Quenching: Air or pressurized gas. For air cooling, cool in still air to 150-125°F (66-51°C).
Tempering: Temper immediately after quenching. Typical tempering temperature is 300°F (149°C) for maximum wear resistance. Hold at temperature for four hours then air cool to ambient temperature.
For maximum toughness, double temper, 2 hours plus 2 hours, at temperatures above 900°F (482°C).
Annealing
Annealing must be performed after hot working and before re-hardening.
Heat at a rate not exceeding 400°F per hour (222°C per hour) to 1500-1550°F (816-843°C), and hold at temperature for 1 hour per inch (25.4mm) of maximum thickness; 2 hours minimum. Then cool slowly with the furnace at a rate not exceeding 50°F per hour (28°C per hour) to 1000°F (538°C). Continue cooling to ambient temperature in the furnace or in air. The resultant hardness should be a maximum of 293 HBW.