Premium H13 Hot Work Die Steel
Premium H13 is a premium quality H13 hot work die steel that is designed to meet the highest quality standards in the die casting industry, and to excel in the most demanding hot work tooling applications. Premium H13 is melted using an electricarc furnace, is refined by the argon-oxygen-decarburization (AOD) process and is further enhanced to aerospace quality levels using Vacuum Arc Remelting (VAR). This rigorous melting practice produces an ultra-high level of microcleanliness and coupled with special thermo-mechanical and annealing treatments creates a homogeneous, fine-grained microstructure.
Premium H13 exhibits outstanding impact toughness and resistance to thermal fatigue cracking (heat checking), and will meet or exceed a wide variety of die casting industry specifications, including the requirements of NADCA 207-2006.
Applications: Premium H13 provides the highest performance in typical applications such as inserts, cores and cavities for die casting dies, die casting shot sleeves, hot forging dies, extrusion dies, and plastic mold cavities and components that require high toughness and excellent polishability.
Composition
C | Mn | S | Si | Cr | Mo | V |
0.40 | 0.40 | 0.001 | 1.00 | 5.25 | 1.35 | 1.00 |
Physical Properties
- Density: 0.280 lb/in3 (7750 kg/m3)
- Specific Gravity: 7.75
- Machinability: 65-70% of a 1% carbon steel
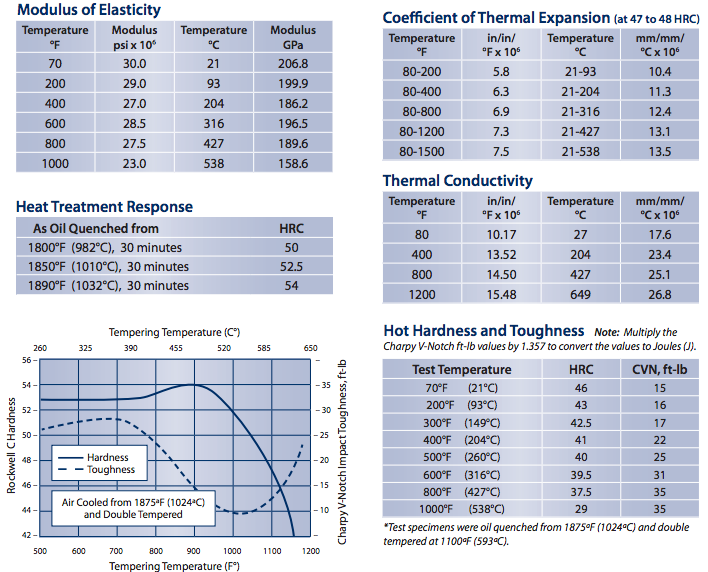
Heat Treating Instructions
Critical Temperatures
Ac1: 1544°F (840°C) | Ac3: 1634°F (890°C) |
Ar3: 1475°F (802°C) | Ar3: 1418°F (826°C) |
Hardening
Preheating: To minimize distortion in complex tools use a double preheat. Heat at a rate not exceeding 400°F per hour (222°C per hour) to 1150-1250°F (621-677°C), then equalize, then raise to 1500-1600°F (816-871°C) and equalize. For normal tools, use only the second temperature range as a single preheating treatment
Austenitizing (High Heat): Heat rapidly from the preheat. Furnace or Salt Bath: 1800-1890°F (982- 1032°C). For maximum toughness, use 1800F (982°C). For maximum hardness and resistance to thermal fatigue cracking and wear use 1890°F (1032°C). Soak at temperature for 30 to 90 minutes.
Quenching: Air, pressurized gas or warm oil. Section thicknesses up to and including 5 inches (127mm) will typically fully through harden when cooled in still air from the austenitizing treatment. Sections greater than 5 inches (127mm) in thickness will require accelerated cooling by using forced air, pressurized gas, or an interrupted oil quench to obtain maximum hardness, toughness and resistance to thermal fatigue cracking.
For pressurized gas quenching a minimum quench rate of approximately 50°F per minute (28.5°C per minute) to below 1000°F (538°C) is required to obtain the optimum properties in the steel. For vacuum heat treatment of die casting die components, the heat treatment practices detailed in the latest revision of NADCA 207 are strongly recommended. For oil, quench until black, about 900°F (482°C), then cool in still air to 150-125°F (66-51°C).
Tempering: Temper immediately after quenching. The typical tempering range is 1000-1150°F (538-621°C). Hold at tempering temperature for 1 hour per inch (25.4 mm) of thickness, 2 hours minimum, then air cool to ambient temperature. Double tempering is required.
Annealing
Annealing must be performed after hot working and before rehardening.
Heat at a rate not exceeding 400°F per hour (222°C per hour) to 1575-1625°F (857-885°C), and hold at temperature for 1 hour per inch of maximum thickness; 2 hours minimum. Then cool slowly with the furnace at a rate not exceeding 50°F per hour (28°C per hour) to 1000°F (538°C). Continue cooling to ambient temperature in the furnace or in air. The resultant hardness should be a maximum of 235 HBW.