Lescowear™ Cold Work Tool Steel
Lescowear cold work tool steel is a versatile medium-chromium, air-hardening tool steel that is characterized by a very good combination of toughness and wear resistance. It is available primarily in round bar forms for cold work tooling applications which demand better toughness but comparable wear resistance compared to D2 cold work tool steel and M2 high speed steel. A similar grade that is available primarily in flat and sheet product forms is LSS™ PGK.
APPLICATIONS: Punches, blanking dies, thread roll dies, coining dies, drawing dies, upsetting dies, and rolls.
Composition
C | Mn | Si | Cr | W | Mo | V |
1.13 | 0.30 | 1.20 | 7.75 | 1.10 | 1.55 | 2.40 |
Relative Properties
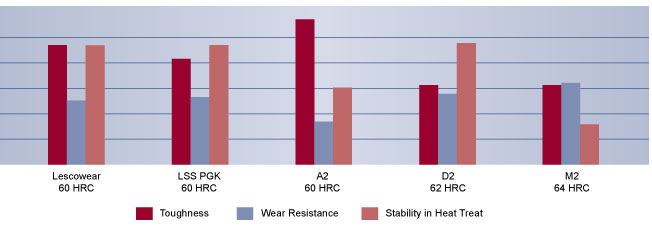
Physical Properties
- Density: 0.281 lb/in3 (7778 kg/m3)
- Specific Gravity: 7.78
- Modulus of Elasticity: 30 x 106 psi (207 GPa)
- Machinability: 50-60% of a 1% carbon steel
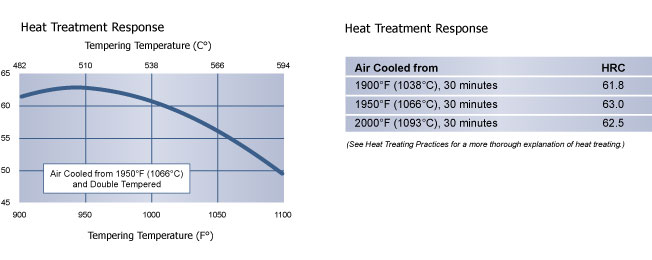
Heat Treating Instructions
Hardening
Preheating: To minimize distortion and stresses in large or complex tools use a double preheat. Heat at a rate not exceeding 400°F per hour (222°C per hour) to 1150-1250°F (621-677°C) equalize, then heat to 1500-1550°F (816-843°C). For normal tools, use only the second temperature range as a single preheating treatment.
Austenitizing (High Heat): Heat rapidly from the preheat. Furnace or Salt: 1900-2000°F (1038-1093°C)
Equalize and soak at the austenitizing temperature for 30 minutes for pieces up to 1 inch (25.4 mm) in thickness, plus 15 minutes for each additional inch (25.4 mm) of thickness.
For maximum toughness, austenitize at the low end of the recommended range. For maximum wear resistance, austenitize at the upper end of the recommended range.
Quenching: Cool in still to 150-125°F(66-51°C).
Tempering: Temper immediately after quenching. Hold at temperature for 1 hour per inch (25.4 mm) of thickness, 2 hours minimum, then air cool to ambient temperature. Typical tempering temperatures are 950 to 1100°F (510 to 593°C).
Annealing
Annealing must be performed after hot working and before re-hardening.
Heat at a rate not exceeding 400°F per hour (222°C per hour) to 1550-1650°F (843-899°C), and hold at temperature for 1 hour per inch (25.4mm) of maximum thickness; 2 hours minimum. Then cool slowly with the furnace at a rate not exceeding 25°F per hour (11°C per hour) to 1000°F (538°C). Continue cooling to ambient temperature in the furnace or in air. The resultant hardness should be a maximum of 241 HBW.